2023-08-07
Introduction
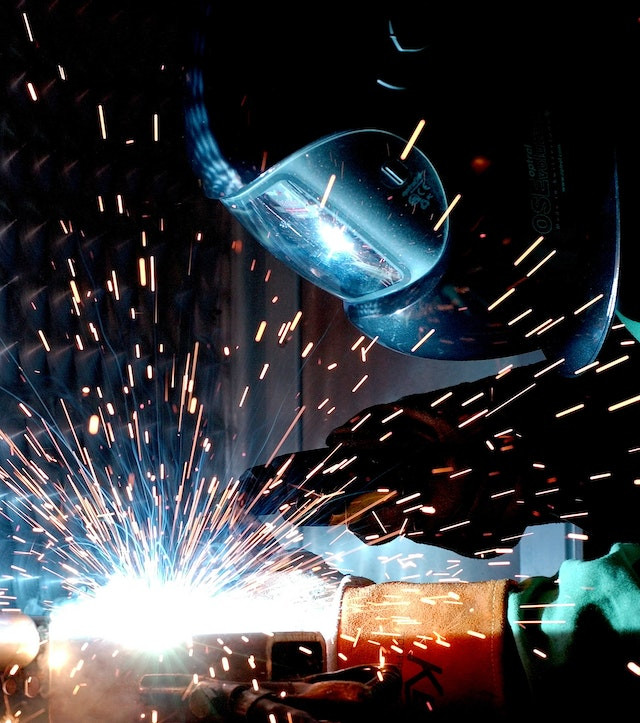
What if you could increase the productivity of your laser cutting machines by 20%? With GaussML's Optimyzer, this is not just a possibility—it's a reality.
In the highly competitive world of sheet-metal manufacturing, improving production quality and efficiency is essential to remain profitable and competitive. The ability to optimize production processes can lead to higher-quality products, increased throughput, and reduced waste, among other benefits. GaussML is helping manufacturing companies improve their production processes with the help of advanced machine learning algorithms.
Our first product, Optimyzer, is a powerful tool that helps machine operators find better settings for their machines. With Optimyzer, manufacturing companies can improve the quality and quantity of their production, resulting in increased efficiency and profitability. Operators of laser cutting machines that use Optimyzer end up cutting 10-20% more, with an improved cut quality. It is for this reason that Optimyzer is becoming increasingly popular among manufacturers, particularly those operating laser cutting machines.
In this article, we will discuss how artificial intelligence (AI) is helping manufacturing companies improve production quality and efficiency. We will explore the challenge of addressing the labor shortage in sheet-metal manufacturing, the importance of laser cutting machine optimization, and the benefits of optimizing sheet-metal manufacturing processes. In the following sections, we provide real-world case studies and success stories to demonstrate how Optimyzer has helped manufacturing companies overcome production challenges and achieve better results.
Get ready to revolutionize your sheet-metal manufacturing with Optimyzer!
Addressing the Labor Shortage in Sheet-Metal Manufacturing
The sheet-metal manufacturing industry is grappling with a significant labor shortage. As experienced workers retire, it is becoming increasingly difficult to find skilled workers to replace them. This shortage of skilled labor has led to increased labor costs, slower production, and decreased efficiency.
To address this problem, manufacturers are increasingly turning to automation tools that enhance worker productivity. Automated programming solutions can convert CAD drawings into machine code for laser cutting machines with minimal human intervention, saving time and reducing the risk of human error. The AI-powered app developed by Optimate (a TRUMPF spin-off) offers a “one-click sheet metal part optimization”. The automated software performs a feasibility check to verify if the part can be manufactured in its current configuration. Their generative AI solution can then automatically suggest design improvements to reduce the cost of manufacturing the part.
Other automation tools can calculate the costs involved in manufacturing a part requested by a customer. The software solution from goCAD lets contract manufacturers provide accurate cost estimates in seconds. It takes into account various factors such as material costs, labor costs, and machine usage costs, and generates an accurate cost estimate for the part. This automation reduces the workload involved in the sales process and allows manufacturers to quickly and accurately provide cost estimates to their customers.
More and more companies are turning to cobots - collaborative robots designed to work alongside humans in manufacturing processes, as they become less expensive. Just like the automated programming and cost calculation tools, cobots can also significantly enhance productivity. They can be used to automate loading and unloading of parts in laser cutting machines and sheet bending machines, freeing up human operators for more complex tasks. For instance, the TruArc Weld 1000 from TRUMPF uses cobots for arc welding tasks, which can significantly increase productivity and reduce the risk of errors. Cobots are a valuable addition to any manufacturing operation.
However, even with these advanced automation tools, there's still a need for skilled operators who can effectively use the machines. The standard settings provided by the machine's manufacturer tend to be quite conservative. That's where Optimyzer comes in. Our AI-assistant empowers every machine operator to perform like an expert. Optimyzer provides machine operators with recommended settings based on machine learning algorithms, reducing the need for specialized knowledge and experience to fine-tune the machine.
Our customers have significantly reduced some of the issues related to labor shortage in sheet-metal manufacturing after incorporating Optimyzer into their processes. For example, one manufacturer was able to keep their production running while an expert operator was on sick leave. A novice operator was able to produce even better cuts after just one day of working with Optimyzer. By making every operator an expert, Optimyzer can help manufacturers overcome the labor shortage and achieve greater efficiency and profitability.
But what makes fine-tuning a laser cutting machine such a complex task? Let's delve into the intricacies of laser cutting machine optimization.
Laser Cutting Machine Optimization
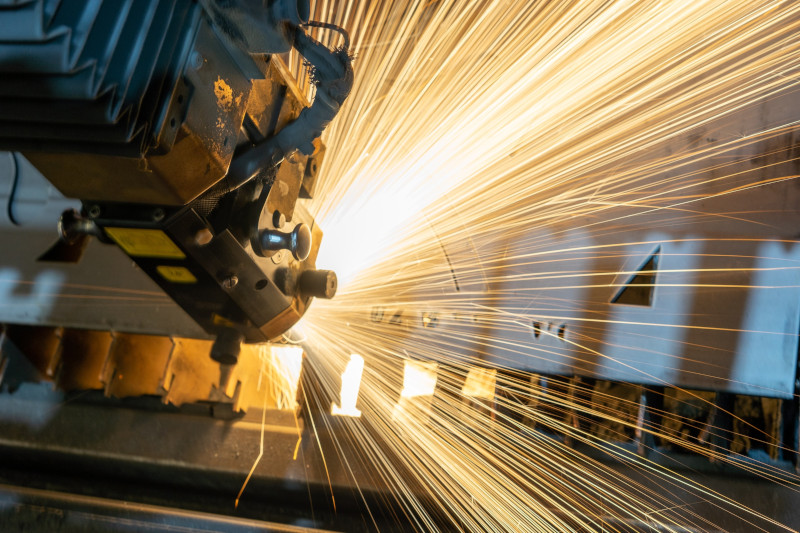
Optimizing the settings of a laser cutting machine can significantly enhance production efficiency and quality. While manufacturers provide conservative settings that work for most applications, these don't necessarily exploit the machine's full potential. That is why laser cutting machine optimization is crucial to remain competitive.
By fine-tuning the machine's settings, operators can achieve faster cutting speeds, improved cut quality, and reduced operating costs. With optimized cutting parameters, operators can produce smoother and more precise cuts, reducing the need for post-processing and improving the overall quality of the finished product. This is especially important in industries where precision is critical, such as aerospace or medical device manufacturing.
Different materials and thicknesses require unique cutting parameters. Depending on the level of automation and the operator's goals - be it increased productivity, reduced burr, reduced gas consumption, or a combination of all - the optimal settings will vary. Optimyzer adapts its suggestions to reach the operator's goals. By using data-driven tools like Optimyzer, operators can quickly and accurately determine the optimal settings for each job, improving efficiency and quality while reducing operating costs.
Factors such as cutting speed, focus position, and gas pressure must be carefully balanced to achieve a clean cut.
The challenge lies in the complexity of the laser cutting process. It involves multiple variables such as material type and thickness, laser power and type, cutting speed, nozzle diameter, nozzle height and gas pressure. Novice operators would rather use the machine with suboptimal settings than try to find the optimal settings without a tool like Optimyzer. Only the top 5% of machine operators have the expertise required to fine-tune the machine with very few experiments.
Optimyzer helps bridge this knowledge gap by making optimization accessible to every operator, regardless of their experience level. It reduces the time and cost involved in the optimization process, while also reaching significantly better results.
Unleashing the Full Potential of Laser Cutting Machines with Optimyzer
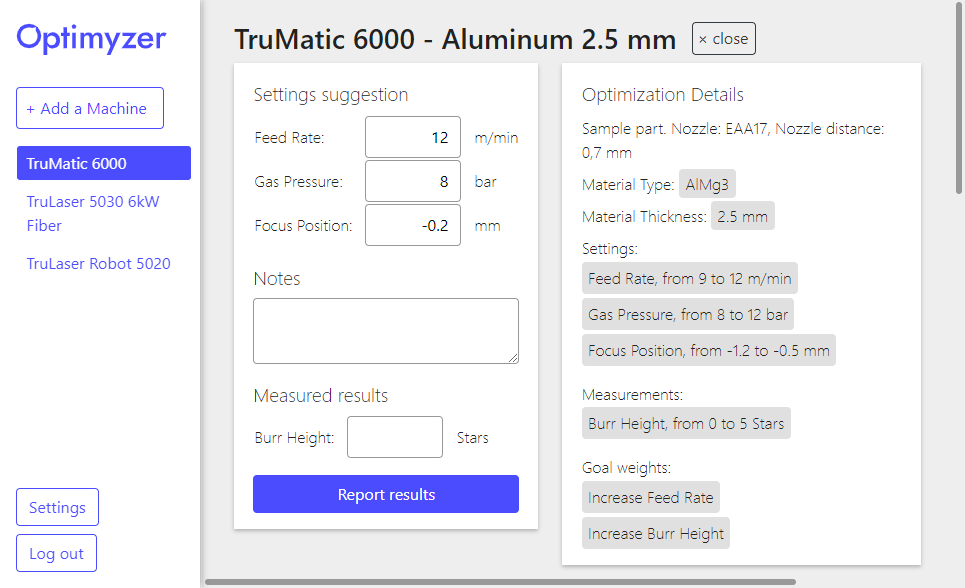
Optimyzer leverages advanced machine learning algorithms to optimize the parameters of industrial machines, and it has proven effective for laser cutting, robotic welding and machining.
Here's how it works:
- The operator creates an optimization for a specific machine and material, setting their preference for production quality, quantity and/or efficiency.
- The operator then tries the settings suggested by Optimyzer on the machine and provides feedback on the results, such as the burr height or surface roughness achieved.
- Based on the feedback, Optimyzer refines its internal model of the machine and makes a new suggestion for the next experiment.
- Steps 2 and 3 are repeated until the operator is satisfied with the results.
With each optimization, Optimyzer becomes more adept at operating the machine, and can quickly optimize it for a new material in under 10 minutes, with just 2 or 3 experiments.
Optimyzer's data-driven approach streamlines the optimization process, reducing the time and cost involved in manual optimization. By leveraging machine learning algorithms, Optimyzer can fine-tune the laser cutting machine's settings with precision, helping manufacturers achieve higher quality cuts and increased production efficiency. For a detailed look at how Optimyzer has improved the production process in real-world scenarios, check out our case studies for laser cutting and robotic welding.
GaussML has already worked with numerous manufacturers, gaining invaluable experience and insights into the challenges involved in laser cutting. Implementing Optimyzer in their production led to a significant improvement in our clients' production quality and efficiency. The table below showcases the range of machines and materials that Optimyzer has successfully optimized, demonstrating our cumulative expertise from over 200 optimizations. This extensive experience across a wide range of machines, power levels, material types, and thicknesses, demonstrates that Optimyzer is a versatile and effective solution for laser cutting machine optimization.
Brand | Power | Material Type | Thickness |
---|---|---|---|
Amada, BLM, Bystronic, HG Tech, LVD, Microstep, Prima Power, Senfeng, Smart Line, TRUMPF | 2kW, 3kW, 3.5kW, 4kW, 4.4kW, 5kW, 6kW, 8kW, 9kW, 10kW, 12kW, 15kW | 1.4016, 1.4301, 1.4404, 1.4571, 1.8714, S235, S235JR, S355, S355JR, S420MC, ST37, ST37E, AlMg3, EN AW-7075 T6, Brinar 400 CR+QT, C100, DD11, DD12 | 0.15 mm, 0.3 mm, 0.5 mm, 1.0 mm, 1.2 mm, 1.5 mm, 2.0 mm, 2.5 mm, 3.0 mm, 4.0 mm, 5.0 mm, 6.0 mm, 7.0 mm, 8.0 mm, 10.0 mm, 12.0 mm, 15.0 mm, 16.0 mm, 20.0 mm, 22.0 mm, 25.0 mm |
Below are a few specific examples of results achieved by our customers thanks to Optimyzer:
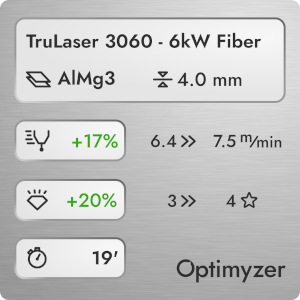
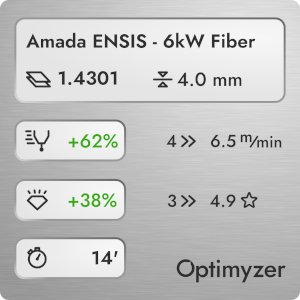
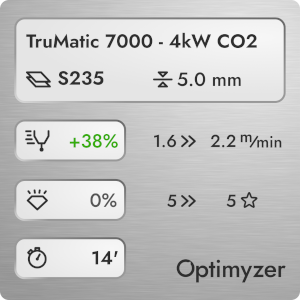
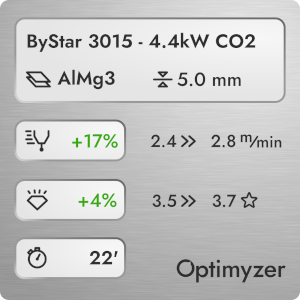
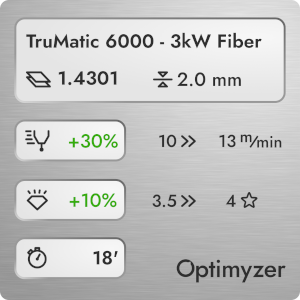
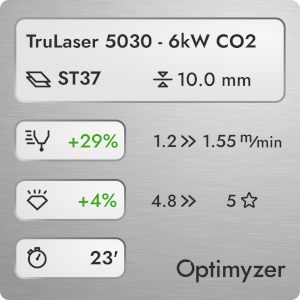
Revolutionize Your Sheet-Metal Manufacturing with GaussML
In the highly competitive world of sheet-metal manufacturing, optimizing your laser cutting machines is crucial to remain profitable and competitive. With Optimyzer, you can achieve faster cutting speeds, improved cut quality, and reduced operating costs. Our AI-assistant empowers every machine operator to perform like an expert, regardless of their experience level.
Optimyzer's data-driven technology streamlines the optimization process, reducing the time and cost involved in manual optimization. We have already worked with numerous manufacturers, gaining invaluable experience and insights into the challenges involved in laser cutting. Implementing Optimyzer in their production led to a significant improvement in our clients' production quality and efficiency.
If you're ready to revolutionize your sheet-metal manufacturing processes, we invite you to get in touch with us. Let's explore how Optimyzer can help you overcome your production challenges and achieve better results. Contact us today to learn more about how Optimyzer can transform your manufacturing processes.
Did you like this article?
Newsletter
The success stories for Optimyzer across new technologies keep growing each month. Don't miss out on opportunities to increase your production's efficiency!
When you sign up for our newsletter, you accept our privacy policy.
You can unsubscribe at any time.