2023-03-21
Introduction
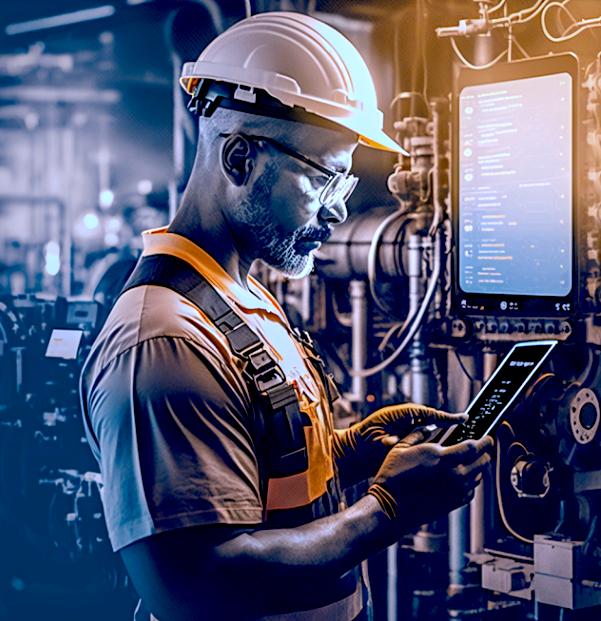
The manufacturing industry is in the midst of a crisis as a result of a severe labor shortage. This issue is likely to only become worse in the coming years. When you are already short on machine operators, anyone going on vacation or coming down with a cold can cause the whole production to shut down. Manufacturing companies that want to remain competitive must also ensure that their products are produced quickly and to the highest quality.
Laser cutting machines are widely used in the sheet-metal manufacturing industry, and optimizing their performance is crucial for meeting production demands. That is easier said than done. But what if you could leverage the power of AI to take your manufacturing processes to the next level? In this blog post, we will discuss the benefits of AI-driven process parameter optimization for sheet-metal manufacturing, which can help overcome these challenges and improve overall efficiency. We will explore how AI technology can optimize laser cutting machine parameters to achieve faster production, higher quality cuts, and reduced waste.
Common Challenges in Finding the Right Machine Settings
In the manufacturing industry, a machine's performance is highly dependent on its configuration. This is especially true for laser cutting machines, which rely on precise parameters to produce accurate and clean cuts. Manufacturers of laser cutting machines usually provide extensive tables of cutting parameters for the most commonly used materials.
Depending on the machine and material quality, achieving a good cut quality might require adjusting the manufacturer's settings. It is up to the machine operators to fine-tune the settings specifically for their own machine and material if they really want to get the most out of their machine. Finding the right machine settings can be a challenging task. Operators are often required to balance multiple factors, such as cutting speed, power, and gas pressure, to produce high-quality parts in a timely manner.
One common challenge that operators face is the sheer number of variables involved in the cutting process. With so many parameters to adjust, finding the optimal settings can be a time-consuming trial-and-error process. This is further complicated by the fact that different materials and thicknesses require different settings, making it difficult to achieve consistent results across different jobs.
Another challenge is the complexity of the cutting process itself. The interaction between the laser beam and the material being cut is highly complex, and even small changes in machine settings can have a significant impact on the quality of the cut. This makes it difficult for operators to predict how changes to the machine settings will affect the final product. In most cases, machine operators can find parameters that lead to a good cut. Only experienced operators are able to find the ideal parameters that simultaneously improve cut quality, increase productivity and reduce cutting costs.
The task of choosing the right machine settings at any time is made even more challenging by the shortage of skilled labor in the manufacturing industry. With a lack of experienced operators, companies may struggle to find personnel who can effectively navigate the complexity of the laser cutting process and make informed decisions about machine settings.
Despite these challenges, there are ways to overcome them and find the right machine settings for laser cutting machines. One solution is to leverage AI-driven process parameter optimization. This new technology helps operators to quickly identify the optimal settings for each job.
How AI is transforming the Manufacturing Industry
You hear about new AI applications practically every other week. The term covers a wide range of technologies that can be used to improve manufacturing processes in a variety of ways. One such application is automated inspection, which uses machine learning algorithms to analyze images of products and identify defects with greater accuracy than human inspectors. This can help reduce waste and improve overall quality.
By leveraging AI to optimize processes, manufacturers can reduce waste, improve quality, and increase overall efficiency.
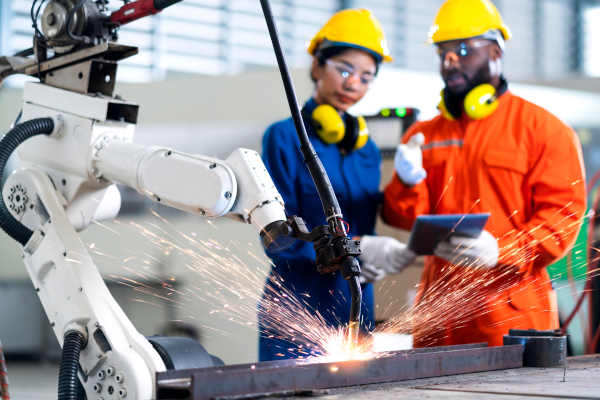
Another area where AI can be particularly useful is in predictive maintenance. By analyzing data from sensors on machines, AI can identify when maintenance is needed and schedule it proactively, reducing downtime and saving money on repairs. Imagine how much money and headaches a manufacturing company can save, if a replacement part arrives the day before the part it is supposed to replace breaks, and not 2 weeks later.
When it comes to optimizing machine parameters, there are various approaches that can be taken. One popular method is using big data approaches like deep learning, which require vast amounts of data from many sensors to learn patterns and optimize performance. This approach can be particularly effective when dealing with complex systems with many variables.
On the other hand, small data approaches like Bayesian Optimization can also be effective for optimizing machine parameters. These methods use statistical models to optimize parameters based on a smaller amount of data, which can be more efficient in certain situations. Ultimately, the approach used will depend on the specific application and available data.
What is AI-Driven Process Parameter Optimization?
AI-Driven Process Parameter Optimization is a technology that uses artificial intelligence algorithms to optimize the process parameters of industrial machines. This kind of AI becomes an expert following a similar iterative learning process than a human machine operator. It involves conducting a series of trial-and-error experiments to learn how the machine works and to find the optimal settings for the machine.
Think of this learning process as looking for the highest peak on a mountainous terrain. The AI starts by trying out a set of parameters, just like a cartographer measuring the altitude on any given point. Then, the operator tells the AI how high that point is, based on how well the machine is cutting. Based on this feedback, the AI builds an internal model of the terrain, with peaks and valleys representing the quality of the cuts produced by different process parameters. The AI then decides which point to measure next, trying to build a better map of the mountain and find its highest peak. The process continues until the AI finds the best process parameters for that particular material and that particular machine. By continuously learning and adapting, the technology can optimize the machine's performance over time and help achieve faster production and higher quality cuts.
Common deep-learning approaches, like the ones you might read about in the news, require large amounts of data from multiple sensors. AI-Driven Process Parameter Optimization is much more efficient and less resource-intensive. Deep-learning approaches require vast datasets to train models like Dall-E or ChatGPT3. These approaches can be expensive and time-consuming to acquire, especially for small and mid-sized manufacturing companies.
In contrast, AI-Driven Process Parameter Optimization employs a more targeted approach that optimizes the process parameters based on the machine operator's feedback, reducing the need for large amounts of data and multiple sensors. This iterative learning process quickly finds the optimal process parameters, significantly reducing the time it takes to reach maximum production efficiency. This results in faster production and better quality cuts, making it an attractive solution for manufacturing companies looking to improve their production efficiency.
Overall, AI-Driven Process Parameter Optimization offers a practical, efficient, and accessible solution for sheet-metal manufacturing companies looking to improve their production efficiency and quality cuts. By optimizing the process parameters based on machine operator feedback, it enables faster results and is easier to implement, making it a valuable technology for companies that want to stay competitive in today's manufacturing landscape.
Benefits of AI-Driven Process Parameter Optimization for Sheet-Metal Manufacturing
Implementing AI-Driven Process Parameter Optimization in sheet-metal manufacturing can lead to numerous benefits, ranging from increased efficiency and productivity to improved product quality and safety. Here are three benefits of using AI-Driven Process Parameter Optimization:
- Increased efficiency and productivity: By optimizing the cutting process parameters, AI can improve the cutting speed and quality, leading to faster production cycles and increased throughput. In one real-world example, a manufacturer of automotive parts was able to increase production speed by 20% by using AI-Driven Process Parameter Optimization.
- Improved product quality: AI can optimize the cutting process parameters to achieve consistent and precise cuts, reducing the need for rework and scrap. This leads to a significant reduction in the cost of rework. For example, a manufacturer of industrial equipment was able to reduce the cost of rework by 30% while increasing production output by 15%.
- Better equipment utilization: By relying on an AI to optimize the cutting process parameters, any downtime caused by operator absence can be avoided. Any operator instantly becomes the most expert operator in the company. This helps maximize the utilization of cutting equipment and increased production capacity.
AI-Driven Process Parameter Optimization can provide numerous benefits to sheet-metal manufacturing facilities, including increased efficiency and productivity, improved product quality, reduced cost of scrap and rework and better equipment utilization. Real-world examples have demonstrated the effectiveness of this technology in achieving these benefits, making it a valuable tool for manufacturers looking to improve their production processes.
Getting Started with AI in Manufacturing: Low-Code and No-Code Solutions
Incorporating AI into manufacturing processes may seem daunting, but there are low-code and no-code solutions that can make it easier to get started. These solutions provide a low barrier to entry for any manufacturing company looking to take advantage of the latest AI advances.
Low-code solutions, as the name suggests, involve minimal coding or programming. Instead, they offer pre-built AI tools and workflows that can be customized and configured to meet specific needs. This allows companies to quickly implement AI-driven process parameter optimization, automated inspection, and predictive maintenance without the need for a team of data scientists or software developers.
No-code solutions take this a step further, allowing users to create AI applications using visual interfaces and drag-and-drop tools, without any coding or programming knowledge required. This makes it possible for even non-technical personnel to create and deploy AI applications within their manufacturing processes.
To start incorporating AI into your manufacturing processes, consider the following actionable steps:
- Identify areas of your manufacturing process where AI could provide the most benefit, such as process parameter optimization, automated inspection, or predictive maintenance.
- Research low-code and no-code solutions that offer pre-built AI tools and workflows for these areas. Look for solutions that offer customization options to meet your specific needs.
- Test out these solutions with a pilot project, starting with a small scope and gradually expanding as you become more familiar with the technology.
- Train your operators on how to use these AI tools and workflows to get the most out of your investment.
By taking these steps, any manufacturing company can start incorporating AI into their processes and reap the benefits of improved efficiency, reduced waste, and higher-quality products. With low-code and no-code solutions, the barrier to entry is low, making it easier than ever to take advantage of the latest AI advances.
Optimizing Manufacturing Processes with Optimyzer
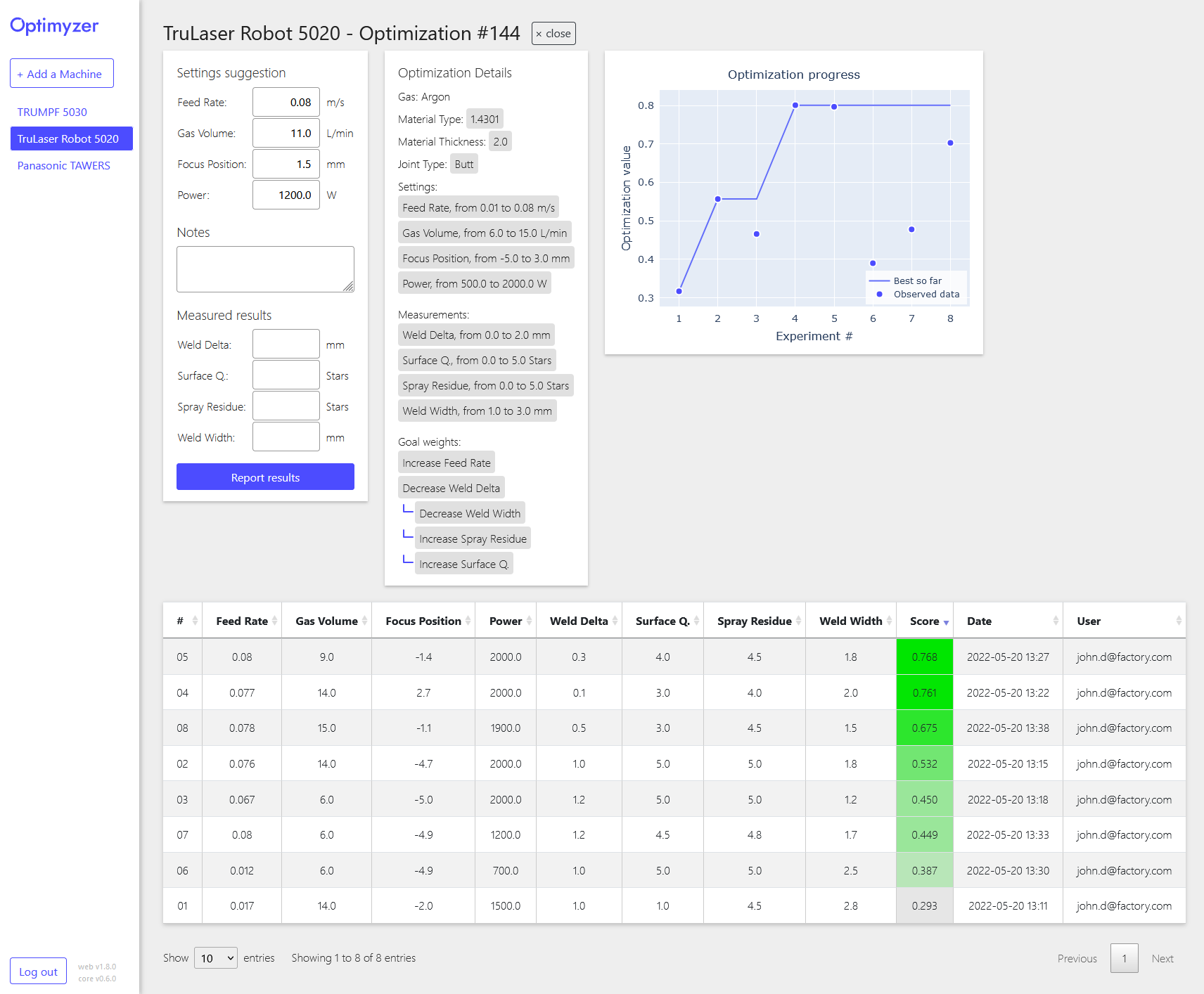
If you're looking for a quick and easy way to incorporate AI-driven process parameter optimization into your manufacturing processes, look no further than Optimyzer. Our AI tool is designed to help machine operators quickly find better machine settings, reducing waste and improving efficiency in the process.
Optimyzer can be used out-of-the-box within minutes, making it even easier to use than a no-code tool. Machine operators simply input the material type and thickness for which they want to find better parameters, and Optimyzer starts making suggestions right away. The operator then runs experiments on the machine to validate the settings, providing feedback to Optimyzer on which settings worked best. Optimyzer learns from this feedback and refines its suggestions for future use. As Optimyzer gets more experience on the machine, it can suggest ideal parameters for additional materials even faster. In many cases, optimizations have been successfully completed in under 3 experiments.
Optimyzer is an AI tool that has already been tested and optimized for the most popular laser cutting machines on the market, including TRUMPF, Amada, Bystronic and Prima Power. Through extensive testing and optimization, Optimyzer has been able to consistently improve the process parameters for these machines, resulting in faster production, higher quality cuts, and reduced waste.
Machine operators have already used Optimyzer to cut a wide range of materials, including stainless steel, mild steel, and aluminum, in thicknesses ranging from under 1 mm to up to 25 mm. By leveraging Optimyzer's AI-driven process parameter optimization, these machine operators have been able to significantly reduce the time and effort required for manual trial-and-error experiments, and achieve better results in less time.
We have designed Optimyzer to be as easy to use as a no-code tool, with no need for advanced programming knowledge or additional hardware. Our solution makes it easy for any manufacturing company to incorporate the latest AI advances into their processes, and start realizing the benefits of improved efficiency and reduced waste.
To start using Optimyzer in your own production, get in touch with us today. Our team of experts will work with you to integrate Optimyzer into your manufacturing processes, and help you start optimizing your process parameters with AI right away. With Optimyzer, you can achieve faster production, higher quality cuts, and reduced waste, while reducing the time and effort required for manual experimentation.
Don't wait to improve your manufacturing processes - contact us today to get started with Optimyzer.
Did you like this article?
Newsletter
The success stories for Optimyzer across new technologies keep growing each month. Don't miss out on opportunities to increase your production's efficiency!
When you sign up for our newsletter, you accept our privacy policy.
You can unsubscribe at any time.